در اسپری درایر، یک مادهی اولیه در یک حلال یا در محلول یک ماده حامل حل، امولسیون یا پراکنده می شود. سپس این ماده اتمیزه می شود و به داخل محفظهی خشک کردن اسپری می شود، جایی که جریانی از گاز خشک کنندهی داغ تبخیر حلال را افزایش می دهد. در ادامهی فرآیند، جامد حاصل توسط نیروهای گریز از مرکز در سیکلون از گاز خشک کن جدا شده و جمعآوری می شود.
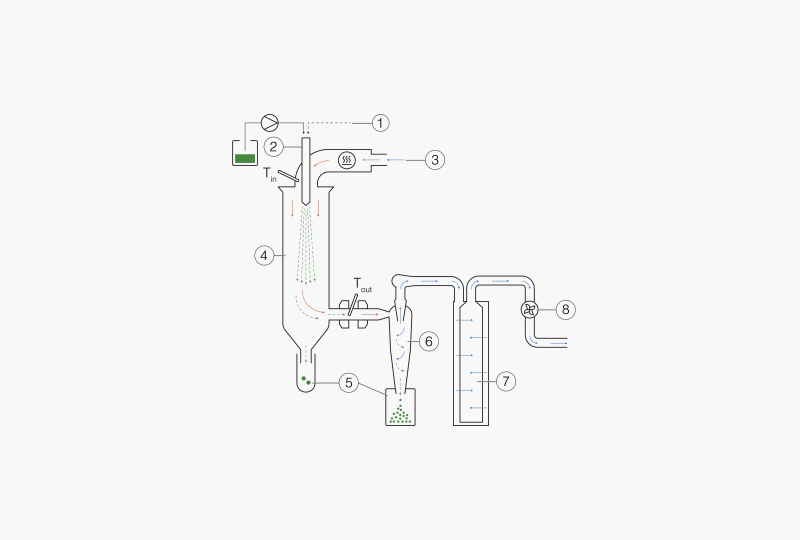
شکل: اصول عملکرد یک اسپری درایر معمولی
① + ② تشکیل قطرات: نازل دو ماده برای S-300
③ گرمایش: گرم کردن هوای تغذیه تا دمای مورد نیاز (حداکثر 250 درجه سانتیگراد)
④ محفظه درایر: تبادل حرارت رسانا بین گاز خشک کن و قطرات نمونه.
⑤ جمع آوری ذرات در دو مکان ممکن
⑥ جمع آوری ذرات: فن آوری سیکلون
⑦ فیلتر خروجی: مجموعه ای از ذرات ریز برای محافظت از کاربر و محیط زیست.
⑧ گاز خشک کن: توسط آسپیراتور عرضه می شود
اشکال و ساختار ذرات
همانطور که در شکل زیر نشان داده شده است، خشک کردن اسپری انواع مختلفی از ذرات را تولید می کند. مورفولوژی آنها شامل ساختارهای متراکم، توخالی و متخلخل یا محصور شده با شکل کروی، چروکیده، چروکیده-جمع شده یا سنوسفر (شبیه دونات) است.
به طور کلی، این قانون اعمال می شود که خشک شدن آهسته منجر به ذرات متراکم تر می شود، در حالی که خشک شدن سریع منجر به تشکیل ذرات توخالی می شود.
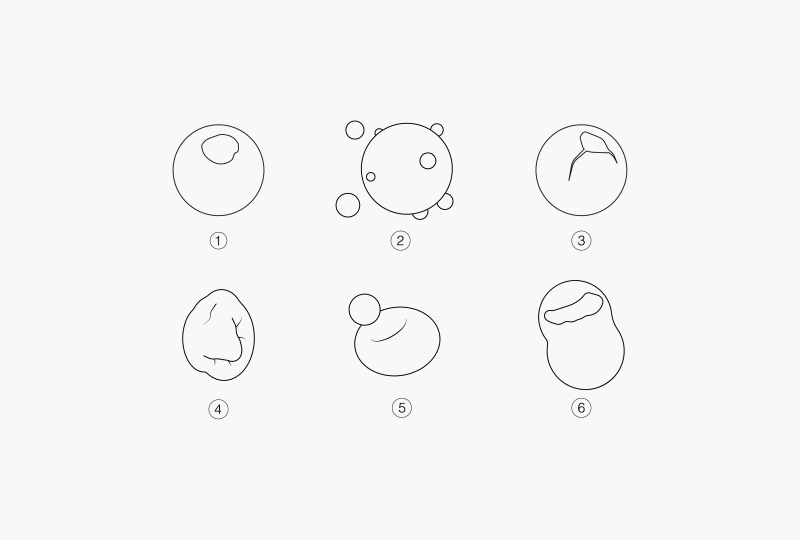
شکل: اشکال ذرات و ساختارهای تولید شده با اسپری درایر
① ذره جامد ② ماهواره ③ ذره توخالی ④ ذره کوچک شده ⑤ سنوسفر ⑥ ذره پوسیده
بهینه سازی فرآیند خشک کردن با اسپری درایر
نتایج به دست آمده با روش اسپری درایر به شدت به خواص مواد، سخت افزار مورد استفاده و همبستگی پارامترهای فرآیند بستگی دارد. این عوامل بر خواص محصول از نظر مورفولوژی، میزان رطوبت باقیمانده و اندازه متوسط ذرات تأثیر می گذارد. بهینه سازی فرآیند معمولاً از طریق “آزمایش و خطا” انجام می شود. با این حال، درک اولیه از فرآیند زیربنایی، استفادهی بهینه از اسپری درایر را به شدت افزایش می دهد.
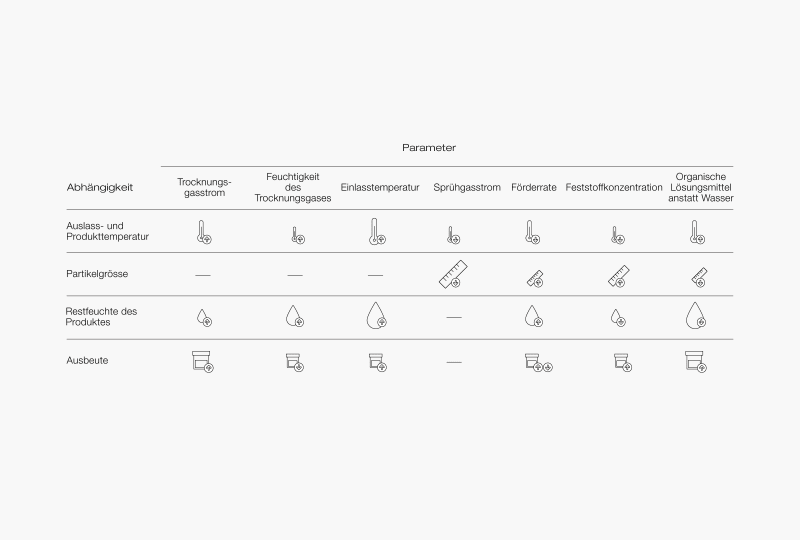
شکل: این جدول وابستگی پارامترهای خروجی (محور عمودی) را در زمانی که یکی از پارامترهای ورودی (محور افقی) افزایش می یابد، نشان می دهد. اندازه شکل تأثیر تغییر را نشان می دهد، فلش جهت را نشان می دهد.
دستورالعملهای کلی برای بهینهسازی اسپری درایر، ریزپوشانی:
پمپ پریستالتیک ماده اولیه را به نازل منتقل می کند. نرخ پمپاژ بر تفاوت بین دمای ورودی و خروجی و اندازه ذرات محصول تأثیر می گذارد:
- سرعت جریان گاز اسپری بالاتر، قطرات کوچکتر و در نتیجه ذرات خشک کوچکتر را فراهم می کند.
- افزایش غلظت مواد جامد در خوراک منجر به ایجاد ذرات خشککنندهی بزرگتر و متخلخلتر میشود که حداکثر غلظت به شدت وابسته به کاربرد است.
· افزایش در نرخ تحویل با یک توان عملیاتی ثابت گاز اتمیزه کننده منجر به افزایش اندازه قطرات می شود.
هرچه توان عملیاتی بالاتر باشد، انرژی بیشتری برای تبخیر قطرات به ذرات جامد مورد نیاز است. بنابراین، در شرایط مشابه، دمای خروجی کاهش می یابد. اگر میزان تحویل خیلی زیاد باشد، ذرات مرطوب و چسبنده تشکیل میشوند و به دیوارهی داخلی محفظه اسپری می چسبند. افزایش دبی باعث کاهش دمای خروجی و افزایش اختلاف دمای ورودی و خروجی می شود.
· کاهش نرخ پمپ در حالی که دمای ورودی و عملکرد آسپیراتور یکسان حفظ می شود، باعث کاهش رطوبت باقی مانده در محصول می شود.
دمای ورودی دمای گاز خشک کن گرم شده است. دمای ورودی بالاتر در صورت دستیابی به توان عملیاتی بالاتر سودمند است. با این حال، دمای ورودی پایین تر باعث حفظ فعالیت ترکیب خشک شده می شود.
دمای خروجی به تعادل گرما و جرم در سیلندر خشک کن بستگی دارد و قابل تنظیم نیست. تحت تأثیر پارامترهای زیر قرار می گیرد: دمای ورودی، سرعت جریان/سرعت آسپیراتور، سرعت جریان، غلظت ماده ای که باید اسپری شود.
سرعت آسپیراتور بالاتر درجه جدایی را در سیکلون افزایش می دهد. با نرخ آسپیراتور کمتر، میزان رطوبت باقیمانده کمتر است.
زمان ماند برای خشک کردن کامل قطرات و کنترل دمای ذرات برای به حداقل رساندن از دست دادن طعم یا تخریب حرارتی ترکیبات حساس به دما مهم است. زمان معمول ماندن در اسپری درایر آزمایشگاهی 0.20 – 0.35 ثانیه است.
دمای انتقال شیشه ای Tg دمایی است که در بالای آن ساختار ماتریس از حالت جامد شیشه ای به حالت لاستیکی و چسبناک تغییر می کند. این اغلب با چسبیدن محصول به دیواره های داخلی شیشه همراه است. دمای بحرانی Tg مخصوص نمونه است. بنابراین، آب به طور قابل توجهی Tg را کاهش می دهد، در حالی که ترکیبات با وزن مولکولی بالا مانند مالتودکسترین در انتقال Tg نمونه به مقادیر بالاتر مفید هستند. به منظور جلوگیری از چسبندگی محصول و مشکلات مربوط به آن، دمای بحرانی Tg نباید در طول فرآیند بیشتر شود.